Research
Following are some of the research projects being pursued in our lab.
The framework of stochastic mechanics is employed to obtain scale-dependent bounds on the response of heterogeneous media (random composites, polycrystals). In doing so, one infers the approach to the Representative Volume Element (RVE), the corner-stone of the separation of scales in continuum mechanics. The RVE is approached by setting up and solving stochastic Dirichlet and Neumann boundary value problems consistent with the Hill(-Mandel) macrohomogeneity condition. Further, the concept of a scaling function is introduced to establish unifying scaling laws. It turns out that the scaling function depends on a mesoscale (scale of observation relative to grain size) and an appropriate metric quantifying the single crystal anisotropy. Based on the scaling function, a material selection diagram is constructed that clearly separates the microscale from the macroscale. Using such a diagram, one can determine the size of RVE for a whole range of polycrystals made of various crystal classes. Application problems include the scaling of the fourth-rank elasticity and the second-rank thermal/electrical conductivity tensors. The trends in approaching the RVE for planar conductivity, linear/non-linear (thermo)elasticity, plasticity, and Darcy permeability is also established.
The impact of this research lies in the fact that one can establish scaling laws that seamlessly integrate the microscale to the macroscale. Such a methodology can be used to understand and predict the properties of a variety of materials. In turn, this will enable the design of novel microstructures with target properties (enhanced strength, stiffness, conductivity and buckling resistance). Such microstructures can then be engineered to build low cost applications that are light in weight and safer.
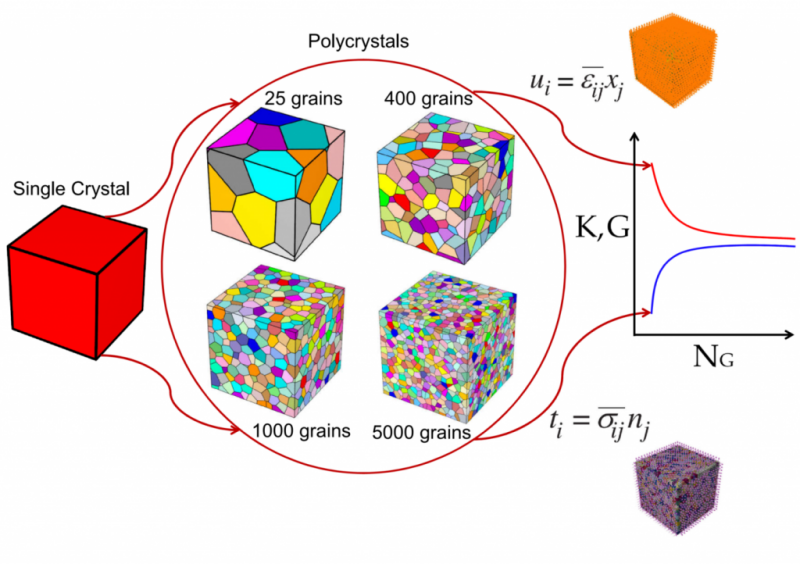
The cost associated with the treatment of Prosthetic Joint Infections (PJI) is expected to reach $ 1.62 billion by 2020, in United States alone. The current gold standard for treatment of infection after total knee arthroplasty is a 2-stage process whereby the implant is removed and temporary spacer made of PMMA (bone cement) with antibiotics is inserted. The patient receives a 6-8 week course of intravenous antibiotics, and then returns to surgery for a re-implantation of a new joint replacement. Unfortunately, PMMA as a drug delivery material has limitations in terms of mechanical and drug-eluting properties. Furthermore, the polymerization reaction for PMMA is highly exothermic, thereby limiting the variety of antibiotics used for the treatment of infections. We have invented a family of 3D printed orthopaedic implants that not only overcome the limitations of PMMA, but can also be designed to be load bearing and customized to individual patient needs. Our implants are smart since they incorporate built-in design features such as micro-channels and reservoirs that enable them to act as antibiotic delivery vehicles. We have filed for a patent with USPTO and efforts are ongoing to commercialize our invention. From the perspective of fundamental science, our invention must necessary comply with the competing requirements stemming from both mechanics and biological perspectives. We have ongoing experimental and computational research that include–a) static and fatigue testing of implants; b) controlling the elution of drugs through the implant; c) bacterial kill studies to assess the effectiveness of eluted antibiotics and d) understanding the effect of manufacturing conditions on the functionality of antibiotics.
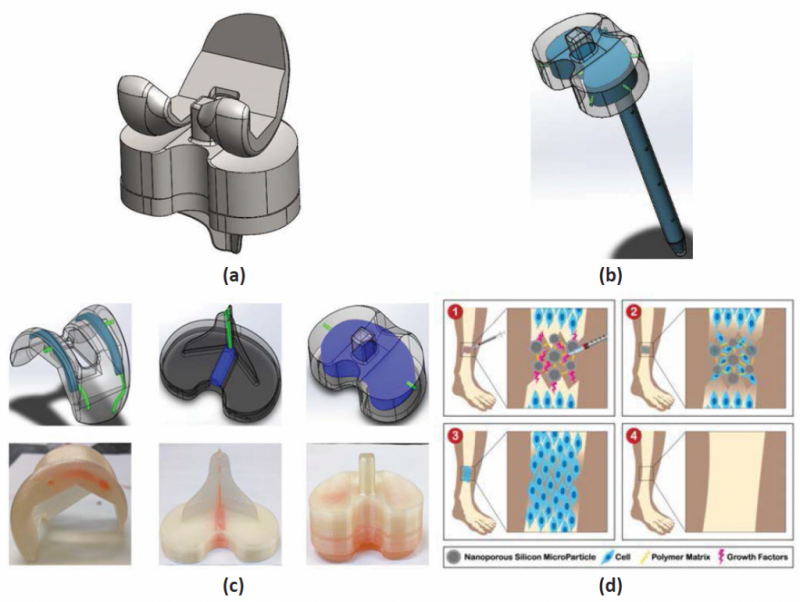
1) Material anisotropy–application to elastic crystals:
Practically all elastic single crystals are anisotropic, which calls for an appropriate universal measure to quantify the extent of anisotropy. A review of the existing anisotropy measures in the literature leads to a conclusion that they lack universality in the sense that they are non-unique and ignore contributions from the bulk part of the elastic stiffness (or compliance) tensor. Proceeding from extremal principles of elasticity, a new universal anisotropy index is introduced that overcomes the above limitations. Furthermore, special relationships between the proposed anisotropy index and the existing anisotropy measures for special cases are established. A new elastic anisotropy diagram is constructed for over 100 different crystals (from cubic through triclinic), demonstrating that the proposed anisotropy measure is applicable to all types of elastic single crystals, and thus fills an important void in the existing literature.
2) Material anisotropy–application to biological materials:
Anisotropy is an essential attribute exhibited by most biological materials. Based on the recent work on anisotropy of a wide range of crystals and polycrystals, we propose an appropriate measure (A) to quantify the extent of elastic anisotropy in biomaterials by accounting the tensorial nature (both stiffness-based and compliance-based) of their elastic properties. Next, we derive a relationship between A and an empirically defined existing measure. Also, the preceding measure is used to quantify the extent of anisotropy in select biological materials that include bone, dentitional tissues, and a variety of woods. Results indicate that woods are an order of magnitude more anisotropic than hard tissues and apatites. Finally, based on the available data, it is found that the anisotropy in human femur increases by over 40 % when measured between 30 % and 70 % of the total femur length.
3) Geometrical anisotropy:
Particle shape plays a crucial role in the design of novel reinforced composites. The notion of a geometrical anisotropy index `A‘ is introduced to characterize the particle shape and its relationship with the effective elastic constants of biphase composite materials is established. The analysis identifies three distinct regions of `A‘: i) by using ovoidal particles with small `A‘, the effective stiffness scales linearly with `A‘ for a given volume fraction a; ii) for intermediate values of `A‘, the use of prolate particles yield better elastic properties; and iii) for large `A‘, the use of oblate particles result in higher effective stiffness. Interestingly, the transition from ii) to iii) occurs at a critical anisotropy `Acr‘ and is independent of a.
Both forms of anisotropy (material and geometric) have applications in a wide range of disciplines that include geophysics, biological materials [see Fig. (a)], diffusion tensor imaging, phase transformations, dislocation dynamics, condensed matter physics and composite materials. For instance, using stiffer ellipsoidal fillers as reinforcement in a softer matrix generates a composite material with properties superior than a similar composite reinforced with spherical fillers [see Figs. (b), (c)]. Further, material anisotropy plays a very important role in seismology with applications to petroleum exploration/production and in the understanding of lower mantle composition and behavior [see Fig. (d)].Particle shape plays a crucial role in the design of novel reinforced composites. The notion of a geometrical anisotropy index `A‘ is introduced to characterize the particle shape and its relationship with the effective elastic constants of biphase composite materials is established. The analysis identifies three distinct regions of `A‘: i) by using ovoidal particles with small `A‘, the effective stiffness scales linearly with `A‘ for a given volume fraction a; ii) for intermediate values of `A‘, the use of prolate particles yield better elastic properties; and iii) for large `A‘, the use of oblate particles result in higher effective stiffness. Interestingly, the transition from ii) to iii) occurs at a critical anisotropy `Acr‘ and is independent of a.
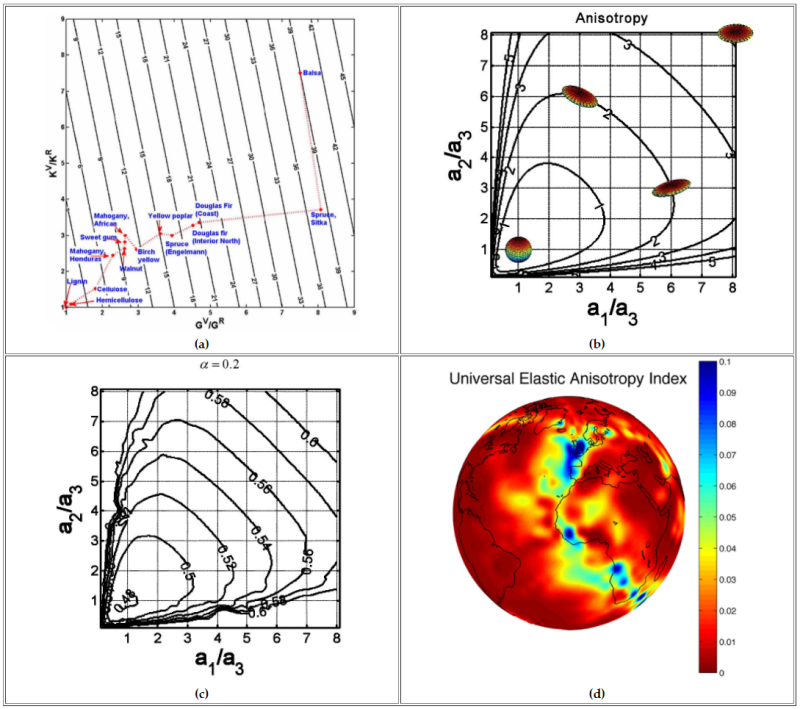
This research is the outcome of a partnership with the U.S. Army Armament Research, Development and Engineering Center (ARDEC). This collaboration enabled access to facilities at Picatinny including materials, equipment, parts, technical support and assisted in the training of undergraduate and graduate students in cutting edge research topics related to 3D printing. The focus of this research was primarily on the ‘Failure of 3D Printed Parts’ in which topics such as printer to printer variation and the effect of infill percentage and pattern on the mechanical properties of 3D printed samples were examined.
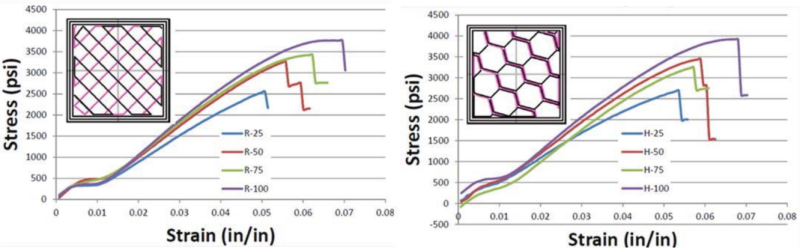